Spis treści
Dźwignia kolankowaCo to jest zawór kulowy?
Zawór kulowy jest zaworem regulującym przepływ, składający się z korpusu zaworu, perforowana i obrotowa kula, i uchwyt. When the handle is aligned with the direction of the pipeline, the valve is open, allowing fluid to flow smoothly through the hole in the ball. When the handle is rotated 90 degrees, the ball’s hole is perpendicular to the pipeline, closing the valve and stopping fluid flow.
The handle’s alignment with the flow direction makes it easy to determine whether the valve is open or closed. Additionally, the valve can be fully opened or closed with just a quarter turn of the handle, making it very convenient and efficient.

Construction of Ball Valves
- Ball valves work by using a ball with a hole through it, which turns inside the valve to control how fluid flows through. When you turn it to fully closed, it creates a reliable seal to stop the flow completely.
- Most ball valves use plastic seats (usually PTFE) that press against the metal ball to create a tight seal. While these plastic seats work well, they can get scratched up when things get too hot. For tougher jobs, some ball valves use metal seats instead – these handle high heat better and won’t get damaged as easily by rough or harsh fluids.
- You’ll find different types of ball valves out there. Some have full-sized holes through them, others have smaller openings, and some even have V-shaped holes. Each type is designed for specific needs, like when you need to control flow really well without losing too much pressure.
- Floating ball valves can come in several body styles, with two-piece, end-entry being the most prevalent, and they are commercially manufactured in sizes up to 24 inches, although practical applications typically utilize sizes up to about 12 inches.
Key components of brass ball valves
- Brass Ball valves consist of a spherical disc (the ball) that rotates within the valve body to control fluid flow, providing a tight seal when fully closed.
- The valve body style can vary, including designs such as split-body, top-entry, and end-entry, each serving different maintenance and access needs.
- Two-piece ball valves feature a main body and one end connection, allowing for some repairs after removal from service, but may face challenges due to galling in the threads.
- The design of three-piece ball valves allows for easy removal of the main body for cleaning or repairs without disconnecting the pipe connectors.
- The valve components and configurations are critical for ensuring effective operation in various industrial applications, including liquid and gas control systems.

Mechanisms of operation
- Brass Ball valves operate using a spherical element (the ball) that rotates within the valve body, allowing or blocking fluid flow through a bore that can be aligned either parallel or perpendicular to the flow direction.
- The simplest manual operation of a ball valve is achieved through a wrench or lever, applying torque to rotate the valve by 90 degrees to either open or close it.
- Some ball valves can be equipped with actuators that may be pneumatically, hydraulically, or motor-operated, providing the capability for both on/off control and flow modulation.
- In normal operation, the ball within a ball valve can float slightly downstream, which compresses the seating mechanism and enhances sealing effectiveness during use.
- A unique feature of certain ball valve designs is a failsafe mechanism wherein the ball can float to the metal body of the valve during extreme conditions, ensuring a secure seal to prevent leaks.
Types of Ball Valves

- There are several types of ball valves, including full port, standard port, and reduced port, each catering to different flow and pressure requirements in various applications.
- By Construction Design
- Full Port Ball Valves:
Full port ball valves, also known as full-bore ball valves, have a bore diameter equal to the connected pipeline, allowing for minimal friction and pressure loss and optimizing fluid flow. - Reduced Port Zawory kulowe:
It features a smaller bore size than the pipe diameter and is suitable for applications where flow restriction is acceptable or desired. - 3-Way Ball Valves:
Designed for flow diversion or mixing, it is commonly used in temperature control systems and process applications. - Trunnion-mounted ball valves:
Trunnion-mounted ball valve is the heavy-duty one. They have extra support(Trunnion) at the top and bottom of the ball, which helps them handle high pressure and heavy flow. The ball stays fixed in place and just spins, with springs pushing the seals against it to prevent leaks.

- By Body Construction
- 1-Piece Ball Valves:
- 1-piece ball valve’s body is made as a single, seam-free unit, which improves sealing and lowers the possibility of leaks. Vacuum systems use it extensively.
- It is the most cost-effective choice among ball valves because of its straightforward construction, which allows for one-step manufacturing. Nevertheless, the one-piece ball valve is disposable since it cannot be repaired and must be replaced completely in the event of damage.
- One-piece ball valves are typically lightweight and small, which makes them appropriate for pipelines with a small diameter. The majority of mini valves are one-piece ball valves.
- 2-Piece Ball Valves:
- Valve seat and a valve cover make up the split-body design of the 2-piece ball valve.
- This kind of valve is the most widely used ball valve because of its straightforward design and affordable price. Even though the threads connecting the valve seat and cover allow for disassembly, thread wear from disassembly and reassembly can impair sealing performance. Repairs and reuse are therefore discouraged.
- Bidirectional fluid flow is possible with 2-piece ball valves, which are simple to install and don’t require a specific installation direction.
- 3-Piece Ball Valves:
- A main body and two pipe connections—usually made with threaded, welded, or flanged connections—make up a three-piece ball valve.
- Systems that need frequent cleaning and maintenance can benefit from this design’s ease of disassembly. It makes it possible to clear the internal walls and remove obstructions from the pipeline.
- In specialized industries like oil, chemical, metallurgy, power, and pharmaceuticals, 3-piece ball valves are widely utilized in high-cycle and high-pressure applications. Three-piece ball valves are also the priciest choice because of their intricate design and large number of parts.

Valve Bore Size: Full Port vs. Reduced Port
Explanation of full port ball valves
- When the valve is open, full port ball valves guarantee unhindered flow because of their large ball, which has the same diameter as the pipeline.
- These valves work well in systems with high flow coefficients and low-pressure drops and are typically used in throttling applications.
- Full port ball valves are ideal for fluid flow because of their bore design, which reduces friction and pressure loss.
- Full port ball valves are simpler to maintain and clean.
- Due to the above advantages, diameter ball valves are more expensive than reduced-diameter ball valves
Explanation of reduced port ball valves
- Reduced port ball valves, also known as reduced bore ball valves, feature a smaller passage for flow, creating a pressure drop in the pipeline as they allow flow through the valve that is one pipe size smaller than the valve’s pipe size.
- The internal diameter of reduced port ball valves is smaller than the pipe diameter, leading to a more restricted flow, which is especially notable in large-scale applications.
- because of the simple structure, reduced port valve production cost is lower than full port ball valves, it can provide a cost-effective alternative to piping systems with low flow requirements. In terms of design, most ball valves—including those that are one-piece—feature a reduced bore, which introduces some friction losses in the system, though these losses are relatively small compared to other types of valves.
- Reduced bore ball valves are commonly used in low-flow piping systems and confined installation spaces.
Brass Ball Valve Features
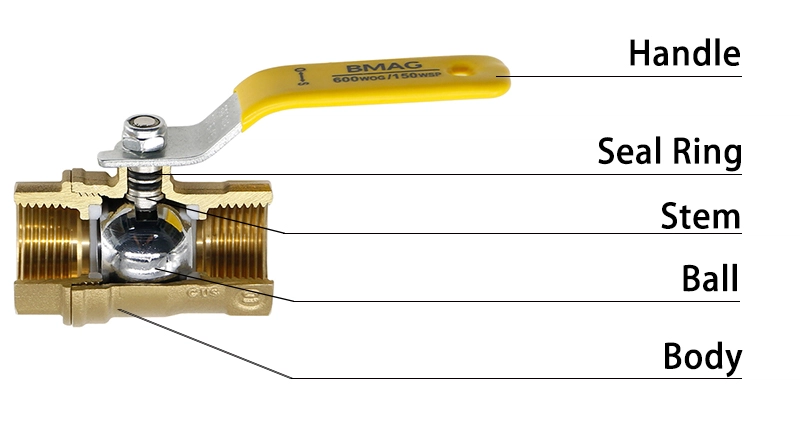
The cross-section view of a ball valve allows us to better understand its internal structure.
BMAG’s brass ball valves offer several advantages:
- Excellent corrosion resistance
- Cost-effective solution
- Suitable for water, olej, and gas applications
- Temperature range: -20°C to 150°C
- Pressure ratings up to PN25
- Available in sizes from 1/4″ to 4″
Key Components:
- Body: High-quality forged brass
- Ball: Chrome-plated brass
- Stem: Blow-out proof design
- Seats: PTFE for superior sealing
- O-rings: NBR or EPDM options
Actuation Methods
- Actuation Methods Ball valves can be actuated using various methods, including manual, pneumatic, electric, and hydraulic actuation, depending on needs.
- Electric actuators provide automated control and can be adapted to a wider range of applications, also more expensive than pneumatic actuators.
- Pneumatic actuator is the conversion of the energy of compressed gas into mechanical motion to regulate the control elements. Motorized ball valves utilize an electric motor to open or close the valve, with the actuator rotating 90° to control the valve’s position based on electrical signals.
- Compliance with the ISO-5211 standard is essential for actuator mounting, ensuring uniformity in dimensions and facilitating the integration of automation systems in ball valve applications.
Ball valves Applications
- The design of ball valves makes them suitable for applications requiring quick shut-off capabilities. Just turn 90 degrees to close the valve completely.
- Compared with gate valves, its closing speed is much faster.
- With types ranging from manual to process and pneumatic ball valves, there exists a variety well-suited for diverse industries including manufacturing, chemical, medical, and food and beverages, are the most used valves.

Oil and gas industry
- Ball valves are essential components in the oil and gas industry, used across upstream, midstream, and downstream applications to control the flow of oil and gas effectively.
Chemical processing
- Ball valves are frequently used in the chemical processing industry to regulate the flow of chemicals, acids, and other corrosive materials within processing facilities.
- Corrosion-resistant materials, such as stainless steel, are commonly employed in ball valve construction to ensure longevity and reliability when handling aggressive chemicals.
Water management
- Ball valves are commonly used in water and wastewater management to regulate the flow in treatment plants and distribution systems.
- Utilizing certified ball valves that meet safety approvals, such as WRAS and DVGW, is essential for applications involving drinking water.
HVAC systems
- Ball valves are commonly used in HVAC systems to effectively regulate the flow of hot water or chilled water.

Ball Valve Selection Criteria
When choosing a ball valve, consider:
- Operating Pressure and Temperature
- Media Compatibility
- Flow Requirements
- Installation Space
- Maintenance Needs
- Cost Considerations
Quality Assurance
- 100% pressure testing
- Material certification
- Dimensional inspection
- Function testing
- Quality control documentation
Special Features Available:
- Anti-static design
- Extended stem options
- Locking handle
- Actuator mounting pad
- Special materials and coatings
Why Choose BMAG Ball Valves?
- Manufacturing Excellence:
- ISO 9001 certified production
- Advanced testing facilities
- Strict quality control
- 20+ years of experience
- Customer Support:
- Technical consultation
- Custom design solutions
- Fast quotation service
- Comprehensive documentation
- Global Service:
- Worldwide shipping
- Multi-language support
- After-sales support
Need Expert Advice?
Our engineering team is ready to help you select the perfect ball valve for your application.Contact us for:
- Technical specifications
- Custom requirements
- Price quotations
- Free sample requests